The COVID-19 crisis is having a devastating impact on world trade. Businesses in many regions are facing unprecedented supply chain disruptions due to lockdowns, factory shutdowns, scaled back production, export and import limitations, restrictions on transport and logistics, and other factors.
During April 2020, India’s exports contracted for the second month in a row, plummeting by 60.28% to $10.36 billion. Imports also fell, by 58.65% to $17.12 billion. This led to a trade deficit of $6.76 billion – the lowest on record in almost four years.[1]
In this challenging environment, it’s critical for trade management and compliance teams to operate with maximum efficiency and agility, while making sure that all rules and regulations are met to keep supply chains moving as smoothly as possible. Right now, companies can’t afford additional and unnecessary delays at customs.
However, as governments adjust their policies in response to the pandemic, trade compliance is more complex to manage than ever. Companies need to stay on top of continuous regulatory changes, across all relevant jurisdictions; and swiftly assess how these impact business.
Managing HS Codes
One of the riskiest aspects of global trade compliance is managing the Harmonized System of Tariff Classification (HS). This internationally standardized scheme, developed and maintained by the World Customs Organization (WCO), is used to determine which tariffs apply and how much duty should be paid when goods move across borders. All exporters and importers are legally required to classify their products under the correct codes. A sound product classification approach not only ensures compliance, but also enables businesses to access relevant exemptions and benefits which are tied to specific HS codes.
The Indian Trade Clarification (ITC) system uses 8-digit codes that are based on the current HS schedule. This can be a complicated scheme to manage, as HS/ITC codes are never static. Regulatory updates to the tariff schedule happen often. Recently, for example, the WCO and World Health Organization (WHO) established a coordinated approach in response to the pandemic; and jointly updated the HS Classification Reference for COVID-19 Medical Supplies. This has been subsequently expanded to cover a greater range of HS-coded medical equipment and critical supplies.[2]
Beyond keeping pace with updates to all relevant product classification code schedules, trade professionals also need to consider how developments within their own businesses impact their classification approaches. When a new product is created or an existing one is modified, for instance, the correct classification information needs to be agreed upon; and internal systems need to be updated.
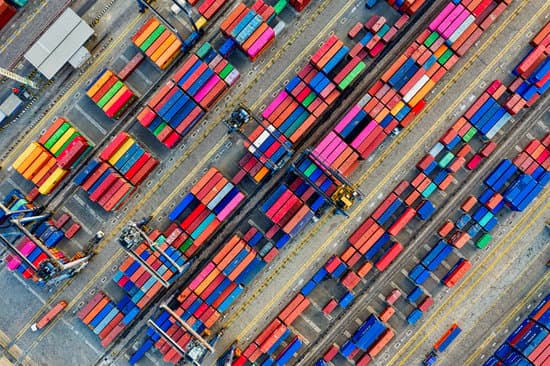
Understanding the risks
Product classification errors or ambiguities can be a major risk factor for cross-border businesses – leading to drawn-out inspection procedures, delays at customs, confiscated goods and eye-watering fines.
Additionally, if a company is found to have misclassified goods, the local customs authority may raise a red flag and the group could be subject to greater scrutiny going forward. It’s not uncommon for authorities to revoke an organization’s Accredited Client Programme (ACP) status or even their Importer Exporter Code (IEC) due to repeat transgressions in this area.
Product classification errors can also result in a company over- or under-paying customs duty. As mentioned, these duties are calculated in relation to specific HS codes. Some product codes, for instance, may have a higher rate of total customs duty due to anti-dumping (ADD) or safeguard duty, depending on the country of origin. The availability of duty drawback (DBK) is also linked to HS codes. If the wrong HS code is used, the wrong DBK amount may be applied, which could lead to a loss of export benefits.
In the current climate, these types of mistakes can quickly erode business resilience.
How can organizations address these problems?
When companies manage their HS/ITC classification schedules manually using paper records and/or spreadsheets, this can make trade compliance more complicated than it needs to be. With this type of approach, every time a government updates the HS schedule, it becomes necessary to amend product classification records manually and share these with all relevant stakeholders across the group and along the supply chain. Sometimes, multinational companies are let down by departments that independently track and execute classification changes with poor communication across the business and to customers. These inefficient approaches can lead to discrepancies, incorrect duty payments, compliance breaches and shipment delays.
One way to resolve these issues, is to implement software that streamlines the HS classification process through automation and data synchronization. This helps to create an efficient, consistent classification system that drives substantial cost and compliance benefits.
Beyond that, a global classification system that leverages artificial intelligence and machine learning can automatically interpret goods descriptions expressed in everyday commercial language to automate classification with a greater degree of accuracy. It can also supply an audit trail for customs, so that compliance teams can demonstrate the processes followed.
Ideally, this software should integrate easily with existing business systems to minimize downtime and stretch the value of existing IT investments.
Are you interested in adding intelligent, automated global classification tools to your technology framework? Get in touch with our global trade management technology specialists today.
References:
[1] https://economictimes.indiatimes.com/news/economy/foreign-trade/covid-19-impact-exports-plunge-60-28-pc-in-april/articleshow/75760239.cms
[1] http://www.wcoomd.org/en/media/newsroom/2020/april/joint-wco-who-hs-classification-list-for-covid_19-medical-supplies-issued.aspx